Comprehensive Guide: What is Porosity in Welding and Exactly How to stop It
Comprehensive Guide: What is Porosity in Welding and Exactly How to stop It
Blog Article
Porosity in Welding: Identifying Common Issues and Implementing Best Practices for Prevention
Porosity in welding is a pervasive concern that commonly goes unnoticed till it creates considerable issues with the honesty of welds. This usual problem can jeopardize the toughness and durability of welded frameworks, presenting safety risks and leading to pricey rework. By understanding the source of porosity and implementing effective avoidance approaches, welders can substantially boost the high quality and dependability of their welds. In this discussion, we will certainly explore the crucial elements adding to porosity development, analyze its detrimental effects on weld performance, and talk about the most effective practices that can be taken on to lessen porosity incident in welding processes.
Usual Sources Of Porosity
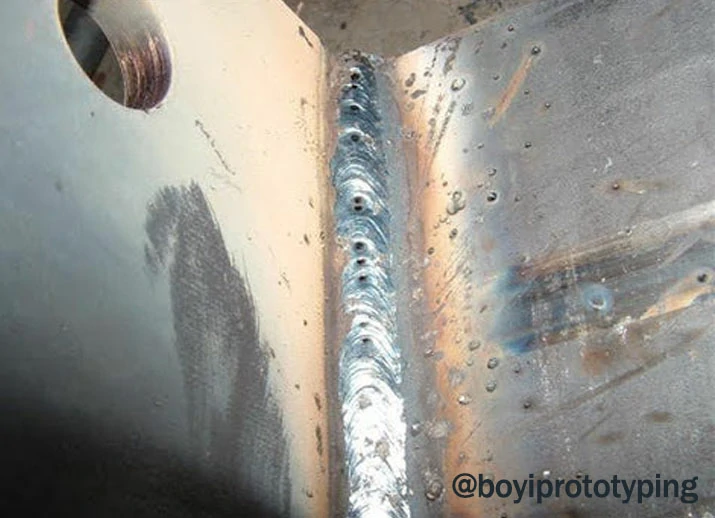
Using unclean or wet filler materials can introduce impurities into the weld, adding to porosity problems. To minimize these usual causes of porosity, complete cleansing of base metals, proper shielding gas choice, and adherence to optimum welding parameters are crucial techniques in achieving top notch, porosity-free welds.
Impact of Porosity on Weld Quality

The existence of porosity in welding can dramatically endanger the architectural stability and mechanical buildings of welded joints. Porosity develops voids within the weld steel, deteriorating its total strength and load-bearing capacity. These voids function as anxiety focus factors, making the weld more vulnerable to breaking and failure under used lots. In addition, porosity can minimize the weld's resistance to corrosion and other ecological variables, additionally lessening its longevity and performance.
One of the main effects of porosity is a decline in the weld's ductility and toughness. Welds with high porosity levels tend to exhibit lower impact stamina and decreased ability to deform plastically prior to fracturing. This can be particularly worrying in applications where the welded elements undergo dynamic or cyclic loading problems. Porosity can impede the weld's capacity to properly send forces, leading to early weld failure and potential safety risks in crucial structures. What is Porosity.
Finest Practices for Porosity Avoidance
To enhance the architectural integrity and high quality of welded joints, what specific measures can be executed to minimize the occurrence of porosity during the welding process? Porosity prevention in welding is important to guarantee the integrity and stamina of the final weld. One reliable practice is correct cleansing of the base metal, getting rid of any kind of impurities such as rust, oil, paint, or moisture that can cause gas entrapment. Guaranteeing that the welding equipment is in great problem, with clean consumables and ideal gas circulation rates, can also dramatically minimize porosity. In addition, keeping a stable arc and controlling the welding parameters, such as voltage, current, and travel speed, aids develop a consistent weld swimming pool that lessens the danger of gas entrapment. Utilizing the right welding strategy for the specific product being welded, such as adjusting the welding angle and gun position, can even more avoid porosity. Regular evaluation of welds and instant remediation of any type of concerns determined during the welding process are vital practices to stop porosity and produce top notch welds.
Value of Appropriate Welding Strategies
Carrying out correct welding techniques is vital in guaranteeing the architectural integrity and top quality of welded joints, building upon the foundation of efficient porosity avoidance actions. Welding methods directly influence the total toughness read and resilience of the welded framework. One key element of correct welding techniques is keeping the right heat input. Extreme warmth can cause raised porosity because of the entrapment of gases in the weld swimming pool. Conversely, insufficient heat may result in insufficient fusion, creating potential powerlessness in the joint. Furthermore, utilizing the ideal welding specifications, such as voltage, existing, and travel speed, is crucial for accomplishing audio welds with marginal porosity.
Moreover, the choice of welding process, whether it be MIG, TIG, or stick welding, ought to line up with the details demands of the job to make certain optimal results. Correct cleansing and preparation of the base metal, as well as picking the ideal filler product, are additionally necessary elements of skilled welding techniques. By sticking to these finest techniques, welders can reduce the danger of porosity formation and create premium, structurally audio welds.
Examining and Quality Assurance Procedures
Testing procedures are vital to spot and avoid porosity in welding, guaranteeing the strength and resilience of the last product. Non-destructive visit our website testing approaches such as ultrasonic screening, radiographic testing, and aesthetic inspection are generally used to identify prospective issues like porosity.
Carrying out pre-weld and post-weld evaluations is likewise important in keeping quality assurance standards. Pre-weld assessments entail verifying the materials, devices settings, and cleanliness of the job area to avoid contamination. Post-weld evaluations, on the various other hand, analyze the final weld for any type of defects, consisting of porosity, and verify see it here that it meets defined requirements. Executing a thorough quality assurance strategy that includes complete screening procedures and evaluations is critical to lowering porosity issues and ensuring the total top quality of welded joints.
Conclusion
To conclude, porosity in welding can be an usual problem that affects the high quality of welds. By identifying the typical sources of porosity and executing ideal methods for avoidance, such as correct welding methods and testing measures, welders can make sure premium quality and dependable welds. It is vital to focus on prevention techniques to minimize the event of porosity and maintain the stability of bonded frameworks.
Report this page